Hannah Coolidge
North American Oilfields and How We Suck Them Dry
ISSUE 60 | SEE AMERICA | JAN 2016
“But I will give men as the price for fire an evil thing in which they may all be glad of heart while they embrace their own destruction.” - Hesiod, Works and Days
Since prehistoric times, humans have combusted carbon-rich organic material—i.e., life—for energy in the form of heat and labor subsidies: cooking food allows for easier chewing and digestion, and increases the number of calories available per unit of food; charcoal (produced by slowly heating organic material in the absence of oxygen) was used extensively in metallurgy; and coal, of course, powered the steam engines of the industrial revolution before becoming the primary source of electrical energy in the 20th century. Now, oil and gas hydrocarbons are the main source of energy worldwide: for example, about 71% of North American energy consumption comes from oil (41%) and gas (30%).
It’s not clear how much oil, exactly, we’ve taken out of the earth, although the most recent estimate is about 1 trillion barrels. (A barrel of oil is 42 U.S. gallons at 60° F, and contains about 5.8 million Btu of energy.) No one knows, either, how much oil is left, and how much of the remaining oil can even be extracted, given technological limitations. The U.S. Energy Information Administration estimates that world’s proved1 reserves are around 1.6 trillion barrels, but this number depends on self-reporting and is contested. And even if we had an infinite supply of oil, the carbon emissions from its combustion are unsustainable. Extracting hydrocarbons from the ground also has localized environmental costs: fracking, for example, became a hot-button issue when landowners complained of natural gas in their water supply, and a blowout on the Deepwater Horizon drilling rig caused 4.9 million barrels of oil to leak into the Gulf of Mexico.
Still, the labor subsidy supplied by our hydrocarbon consumption is enormous: Nate Hagens, former editor of the Oil Drum, estimated that the energy provided by a single barrel of oil is equivalent to about 25,000 hours of human labor. And so we keep digging.
Conventional Oil
Today’s oil and gas deposits formed in source rock between 350 and 290 million years ago, during the Carboniferous period. Tiny aquatic plants and animals—phytoplankton and zooplankton—died and sank to the bottom of the ocean where they were covered by silt and clay; in this way, layer upon layer of organic-material-rich mud and silt accumulated upon the seafloor. At several hundred feet of depth, the sediment was gently heated and compressed, until the organic material converted into kerogen, a solid, waxy mixture of complex hydrocarbons. Sediment continued to accumulate until it compacted the deepest of these sedimentary layers (thousands of feet below the surface) into fine-grained sedimentary rock (shale, for example). With the right combination of heat and pressure (2,500 to 16,000 feet below the surface, at temperatures between 150° and 300° F), the kerogen within the shale turned to beads of oil and gas by thermal degradation and “cracking”—a process in which longer hydrocarbon chains are broken down into smaller ones—though the petroleum remained trapped in the impermeable shale. And over millions of years more, the rock formations bent and buckled and shifted, distorting the rock layers.
Gas and liquids do not flow easily through source rock and so the expulsion of hydrocarbons from their place of origin is not well understood. But the hydrocarbons do escape (aided by compaction, from the pressure of overlying sediment), squeezing out of the widest apertures in the pore network into the nearest coarse-grained rock formations. Coarse-grained rocks (sandstone, and carbonates such as dolomite and limestone), allow for the unobstructed flow of hydrocarbons: since most rock pores in subsurface sedimentary formations are filled with water, the relative buoyancy of the hydrocarbons causes them to flow upwards, moving through these coarse-grained formations until they reach the earth’s surface and escape, or else become trapped in the subsurface. Oil reservoirs form where the rising hydrocarbons reach some deformity in the rock that prevents them from rising further; hydrocarbons accumulate in the rock pores below the deformity. One form of structural trap is an anticline, a concave fold in the rock strata where the coarse-grained formation is capped by impermeable rock. Another is a fault trap, where the slippage of rock along fault lines brings an impermeable stratum in contact with a permeable one, preventing migration. Stratigraphic traps cause hydrocarbons to accumulate where a change in the local porosity and permeability of the reservoir rock keeps them from escaping. Over millions of years aerobic and anaerobic bacteria eat away at the hydrocarbon chains, with a preference towards lighter and more volatile molecules—older oil reservoirs (and those that are poorly sealed against microbes) therefore contain heavier, more viscous crude varieties.
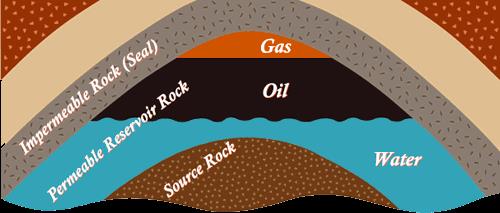
Anticline trap.
Pockets of oil stored in these subsurface reservoirs are “conventional” oil sources, and have provided North America with many billions of barrels of oil since large-scale commercial extraction began in the 1870s. But the conventional oil resources of North America are in decline: it’s likely that the largest conventional reservoirs have already been discovered and most of these are producing less and less each year. U.S. conventional oil production peaked at 9.9 million barrels per day in 1970; Canada’s conventional production peaked at 2 million barrels per day in 1973; and Mexico’s production peaked at 3.4 million barrels per day in 2004.2
There is still plenty of conventional oil to be produced. There’s just not as much as there was, and it’s not enough to meet demands. Alaska’s North Slope (which includes the supergiant Prudhoe Bay Oil Field, which has produced over 12 billion barrels of oil since 1977) still has an estimated remaining 3 billion barrels of recoverable oil, while offshore proved reserves in the Federal Gulf of Mexico are about 5 billion barrels. The U.S. Geological Survey estimates that there are an additional 58 billion barrels of “undiscovered, technically recoverable” oil in the Gulf of Mexico, but this estimate is more uncertain. Canada has about 5 billion barrels of proved conventional oil reserves, mostly located in the Western Canadian Sedimentary Basin (which underlies about 540,000 square miles of western Canada) and in offshore reservoirs on the Atlantic, while Mexico’s proved reserves are about 9.7 billion barrels. Mexico has two giant oilfields offshore in the Bay of Campeche, just north of Ciudad del Carmen. Production from the Cantarell Field—once one of the largest oil fields in the world, with about 18 billion barrels of recoverable oil in place when production began in 1981—has declined from a peak of 2.8 million barrels per day in 2004 to around 250,000 barrels per day in 2015; production in the nearby Ku Maloob Zaap field, which also began in 1981, was about 1 million barrels per day in 2015 and has not yet begun to decline. Mexico also has some conventional onshore reserves, notably the Chicontepec Formation to the northeast of Mexico City, which contains 637 million barrels of proved reserves and 15 billion additional barrels of probable and possible reserves. However, this formation presents several technical difficulties: the fields in the formation are highly fractured and at low pressure, making oil difficult to extract at economic rates.
* * *
Conventional oil reserves are exploited by drilling a vertical well into the reservoir rock, sealing the well, and then allowing it to produce oil using the natural drive mechanisms present in the reservoir. Artificial lift may be used to increase well production or compensate for poor reservoir drive: pumps are often used, and sometimes produced water or gas is reinjected into the well to maintain reservoir pressure.3
To begin drilling, a shallow starter hole is first drilled, wider than the planned wellbore, and a large-diameter conductor pipe is driven into the borehole to provide initial structural stability to the well. The bottom-hole assembly—which includes the drill bit, the drill collar (which gives weight to the drill bit) and the drill stabilizer (which keeps the drill bit centered in the hole)—is inserted into the starter hole, and attached to either a top drive or a rotary table (both are mechanical devices that provide clockwise torque to the drill string). As drilling progresses, lengths of hollow drill pipe are added to the assembly to increase the length of the drill string, and drilling fluid (“mud”) is pumped through the hollow drill string to cool and lubricate the drill bit, circulate rock cuttings out of the drill hole through the annulus (the space between the drill string and the outside of the wellbore), and exert downward hydrostatic pressure on the reservoir fluids to prevent oil from flowing up into the well during drilling.
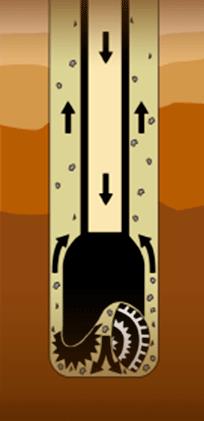
Flow of drilling mud.
If the drill bit enters a reservoir pocket with unusually high pressure, the reservoir pressure may overcome the hydrostatic pressure from the drilling mud, causing formation fluids to flow up into the wellbore. This is called a kick. The drilling mud pressure must be increased, or the well “shut in” by closing the blowout preventer (or BOP, which is installed at the top of the drilling rig) and pumping heavy fluids at high pressure through a choke in the BOP. Otherwise, a blowout will occur, and uncontrolled high-pressure oil and gas will gush out of the well; the pressure of the escaping fluid can be high enough to eject the entire drill string from the well. And blowouts can ignite, either from the heat of friction or from sparks created by rocks ejected from the borehole, causing oil-well fires that are difficult to extinguish.
If all goes smoothly, the well is drilled in sections, and at the completion of each section drilling is resumed with reduced hole size. Well completion is the process of setting steel casing to protect the well, cementing the steel casing in place, and installing a production tree on top of the wellhead to control the oil flow from well to pipeline. Cementing the well provides stability to the formation and prevents hydrocarbons from escaping the wellbore into the subsurface. Once the well is cased and cemented, production tubing (2-4 inches in diameter) is inserted to protect the casing from wear, tear, and corrosion; the tubing also provides a continuous bore from the production zone to the wellhead. If the reservoir is well established, the well may only be cased and cemented to the top of the reservoir, in what is called an open-hole (or barefoot) completion. This procedure saves money on time and materials, but the lower portion of the wellbore (the part within the reservoir) is left unsupported and may collapse. When the well is cased deeper into the body of the reservoir, the casing and cement must be perforated (using a special gun or explosive charges lowered into the well) in order to allow hydrocarbons to enter the well.
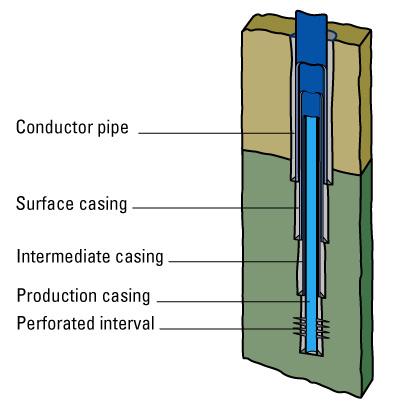
Well casing.
Eventually well production begins to decline. The rate of decline depends on the geology of the oilfield and on the original reservoir drive mechanism: wells with a gas-cap or water drive typically produce at a steady rate until the expanding gas cap or rising water level reaches the production zone, at which point the well suddenly begins to produce large quantities of water or gas and much smaller quantities of oil. Solution gas drive wells typically show an exponential decline in production early on, with the rate of decline decreasing over time.
Enhanced recovery methods can be used to increase production in mature oilfields. Gas injection is the most common enhanced recovery method: a compressed gas such as methane, nitrogen, or carbon dioxide is injected into a reservoir through several specialized gas-injection wells spread systematically throughout the oilfield. Once inside the reservoir, the gas expands, forcing residual oil through the formation and into the well. Gas injection can be used alone or in sequence with water or chemical flushes. About 60% of secondary recovery in the United States is accomplished through gas injection: carbon dioxide injection is particularly common in the declining conventional oilfields of the Permian Basin, in West Texas and New Mexico. (Carbon dioxide injection is used heavily in the U.S. because of the country’s large natural reserves.) The Cantarell Oil Field in the Bay of Campeche is the site of a six-billion-dollar nitrogen injection project, which includes the world’s largest nitrogen-generation plant, capable of supplying 1.5 million cubic feet per day of compressed nitrogen to the oilfield. According to Pemex, the nitrogen injection project will allow the Cantarell Field to produce 2.3 billion barrels more oil than it would otherwise have produced.
Advanced well stimulation techniques include matrix acidizing (injecting hydrochloric acid into a formation to clear clogged pore throats and/or partially dissolve the rock formation to increase permeability); thermally enhanced oil recovery, usually steam injection (which heats the oil, thereby reducing its viscosity and making it easier to extract); and hydraulic fracturing (injecting water at high pressure into the rock to create additional fractures for oil to flow through).
Unconventional Oil
Unconventional petroleum sources are those that cannot be extracted by drilling a well into reservoir rock: these reserves require the use of technology to alter either rock permeability or oil viscosity for commercially viable production to take place.
Tight oil is oil still trapped in its source rock—often the shale formation underlying existing conventional reservoirs. Shale’s low permeability means that oil cannot flow freely through the formation, and so a conventional vertical well would produce little or no oil from the rock. And yet tight oil now accounts for over half of U.S. production, which has increased from 3.9 million barrels per day in 2008 (a historic low) to a peak of 9.5 million barrels per day in 2015. The country’s proved reserves, which now take into account tight oil resources, have increased from 20 billion barrels in 2009 to 39 billion barrels in 2015. The Eagle Ford Shale in southern Texas and the Bakken in North Dakota are the highest-producing shale plays in the country: at its peak, the Eagle ford produced 1.7 million barrels of tight oil per day, while the Bakken produced 1.2 million barrels per day. (Production in both areas has since declined by a few hundred thousand barrels per day, because of the low price of oil on the world market.)
Canada has two major shale plays: the Cardium formation in Alberta, and the Bakken formation which extends into Saskatchewan and Manitoba. In 2014, Canada was producing about 400,000 barrels of tight oil each day from these regions, and Canadian oil companies have identified about 500 million barrels of proved and probable reserves in the country. Mexico, on the other hand, has yet to exploit its tight oil resources, but an estimated 13.1 billion barrels of recoverable tight oil exists in shale formations in the Burgos and Tampico Basins to the northeast of the country. (The Burgos Basin is an extension of the Eagle Ford Shale.)
Tight oil is extracted by horizontal drilling in combination with hydraulic fracturing (“fracking”). Neither technology is particularly new: the first well was fracked in 1949, as an experimental method of conventional reservoir stimulation, and horizontal drilling technology was well-developed by the 1970s. (The first directional drilling was developed much earlier, as a technique for stealing oil from your neighbor’s well.) Horizontal drilling allows broader wellbore access to the reservoir than would be possible with a traditional vertical well, since most rock strata are more or less horizontally oriented. In a frack well, a horizontal borehole is drilled vertically until the drill bit is about 500 feet above the desired rock stratum, at which point the drill string is redirected horizontally into the stratum. Hydraulic fracturing uses the high-pressure injection of water-based fluid to create fractures in the rock surrounding the horizontal wellbore. This is done in stages to concentrate the water pressure on one section of the horizontal wellbore at a time—otherwise, if the well were fractured all at once, the fractures would be uneven and concentrated in the weakest areas of the rock. Fracturing in stages is accomplished by isolating each interval with a mechanical plug, which is then removed once the frack job is complete. The well is then fracked again, this time with some kind of proppant (usually sand) mixed into the frack fluid, which further opens up the fractures and prevents them from collapsing once the injection pressure is removed. In the third phase the well is flushed with frack fluid, again without proppants, to push any proppant remaining in the well out into the existing fractures. Then injection pressure is released and about 20-40% of the frack fluid that was injected into the well flows back to the surface. (The rest of the fluid remains inside the formation.)
Like that of the United States, Canada’s oil production has increased only due to the relatively recent commercial viability of unconventional oil—although in Canada, most of the production increase is from oil sands rather than tight oil. Canada produced about 3.7 million barrels per day of petroleum in 2015, a number which has steadily increased since the early 2000s. (As of 2015 over half of Canada’s oil production came from Alberta’s oil sands and this proportion is only expected to increase.) From 1980 to 2002, Canadian proved reserves were below 10 billion barrels, but spiked to 180 billion barrels after it was determined to be technologically and economically feasible to extract petroleum from the oil sands in Alberta. Now Canada has the third largest proved oil reserves in the world, after Saudi Arabia and Venezuela.
Oil sands are composed of loose sand or partially consolidated sandstone, clay, and water, saturated with an extremely dense and heavy crude oil known as bitumen. Bitumen is so viscous that it will not flow through a well or pipeline unless it is heated or diluted with lighter petroleum products. Oil can be produced from oil sands either by open pit mining or in situ production. Pit mining involves scooping the oil sands into trucks, which then carry the sands to a processing facility where they are mixed with hot water and shaken to separate the bitumen, which is then skimmed off the top in the form of “bitumen froth,” which must be deaerated, processed further to remove more water and solids, and mixed with natural gas or light crude to lower its viscosity for pipeline transport. To extract bitumen from oil sands more than about 200 feet below the surface, in situ production is used; the most common method for in situ oil sands production is steam assisted gravity drainage, in which two horizontal wells are drilled, several feet apart. The upper wellbore is used to inject steam into the oil sands to heat the bitumen, increasing its mobility and causing it to drain into the lower wellbore, where it is pumped out. Another less common in situ production method is cyclic steam stimulation. In this process high-pressure steam is injected for several weeks into a horizontal wellbore in the oil sands, which are loosened by the steam pressure. As the steam saturates the bitumen in the sands, the bitumen melts, and when the steam injection phase is completed the melted bitumen is pumped from the same wellbore. The oil derived from bitumen is considered a “synthetic” crude oil, because of the extreme amount of chemical processing required to turn bitumen into a form of crude acceptable for use in refineries.
The third source of unconventional oil is oil shale, or kerogen shale, which contains hydrocarbons in solid form, which can then be processed into liquid hydrocarbons called shale oil. The Green River Formation in Colorado, Wyoming, and Utah contains the largest oil shale deposit in the world—potentially 3 trillion barrels, maybe half of which could be commercially recovered, although current technology and oil prices do not allow for the large-scale commercial production of shale oil. The hydrocarbons in oil shale are “immature,” still in the form of kerogen, meaning that some biodegradation has occurred, but not enough heat and pressure have yet been applied to turn the kerogen into petroleum. (Shale oil should not be confused with tight oil, which is the mature petroleum extracted from shale through hydraulic fracturing.) Shale oil extraction is usually performed above ground, by mining the oil shale and then treating it in thermochemical processing facilities. In situ extraction methods, which involve heating the oil shale while it is still underground and then pumping the kerogen out once it has liquified, are still in experimental stages.4
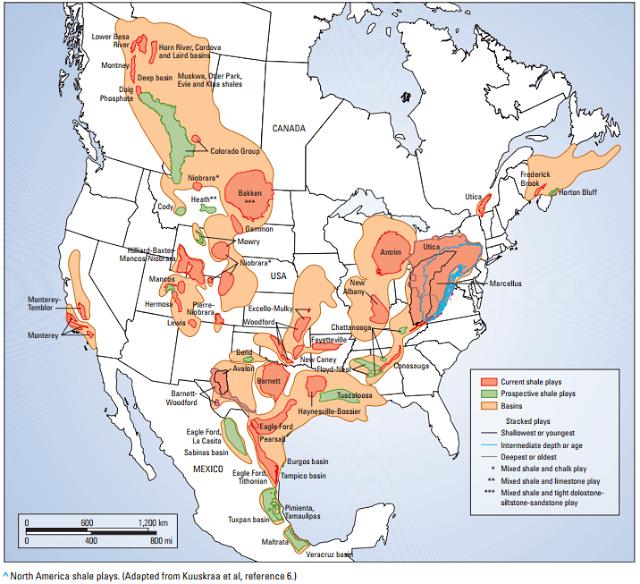
Map of current and prospective shale plays in North America
What’s in a barrel?
Crude oil is a mixture of relatively volatile hydrocarbons (about 84-87 percent carbon and 11-14 percent hydrogen by weight) along with much smaller quantities of sulfur, nitrogen, and oxygen—and it is classified primarily by density and sulfur content: crude that contains less than 0.5% sulfur is considered sweet, while crude containing more than 0.5% sulfur is sour. Low-density (less viscous) crude is light, and high-density crude is heavy.5 The density of the oil depends both on the length of the hydrocarbon chains it contains (shorter hydrocarbons mean lighter oil), and on the ratio of hydrogen to carbon atoms in the oil (a higher ratio of hydrogen to carbon also means that the oil will be lighter).6 Lighter, sweeter oil is generally the most desirable because it is easier to pump, can be more easily refined into higher-value products such as gasoline and diesel, and requires less of the complex refining processes needed to remove sulfur content. (Sulfur is corrosive and potentially toxic in the form of certain compounds such as hydrogen sulfide; when combusted, it also contributes to acid rain.)
On average, a barrel (42 U.S. gallons at 60° F) of light, sweet crude processed in U.S. refineries yields about 19 gallons of motor gasoline, 12 gallons of diesel fuel, 4 of gallons jet fuel, 2 of gallons liquefied petroleum gas (i.e., propane or butane), and 8 gallons of various other petroleum products, including lubricating oils, fuel oils (used for home heating and electric power generation), waxes, asphalt, and petrochemical feedstocks (used to manufacture chemicals, synthetic rubber, and plastics).
The first and most simple refining process is fractional distillation, which separates the hydrocarbon compounds into product streams according to their different boiling points. The crude is heated in a steam boiler to a temperature of about 750° F, where most of the compounds turn to vapor, which enters the bottom of a distillation tower. The towers are filled with trays, which have bubble caps to allow the vapor to pass through them as it rises. The vapor cools as it rises through the tower, and as various compounds in the vapor cool to their boiling point, they condense and fall as liquid into the tray below. The lightest materials, such a propane and butane, rise to the top; medium weight materials, such as gasoline, jet fuel, and diesel fuel, condense in the middle; and heavier compounds called gas oils condense towards the bottom of the tower. Collected liquid fractions are then piped into separate storage tanks to await further processing. The heaviest residual oil that does not vaporize is pumped into a coking unit where it is heated further into vapors and petroleum coke, which is used as a raw material for manufacturing and can be burned as an alternative to coal to produce electricity. The vapors produced from the coking unit feed the next distillation tower, where the process is repeated.
However, fractional distillation (especially applied to heavy crude) produces a smaller proportion of light products, such as gasoline and jet fuel, than the market demands, and so many of the heavier product streams produced by distillation (heavy and medium gas oil, for example) are then transferred to fluid catalytic cracking units and hydrocracking units, where they are broken down, using heat and catalysts, into smaller hydrocarbon chains to produce gasoline, diesel, and jet fuel. As cracking processes create these light transportation fuels, they also break the hydrocarbons into chains that are lighter than gasoline, which must then be recombined into longer gasoline hydrocarbon chains through alkylation (a process also requiring a catalyst). The final conversion method is catalytic reforming, a process that ultimately restructures linear hydrocarbons (paraffins) into cyclic aromatic hydrocarbons, which have higher octane numbers and therefore improve the quality of the gasoline. 7 Then the products are ready for purification: in this process (called hydrotreating), the products are exposed to hydrogen and a catalyst under high temperature and pressure, resulting in hydrogen sulfide and a desulfurized petroleum product. (This process is also used to remove nitrogen from petroleum products.)
Refineries typically blend multiple crude streams to use as feedstock, taking into account the market price of various blends, the refinery’s own particular configuration (toward heavier or lighter crudes), and the demand for specific petroleum products. To process heavy crude, a refinery needs coking units, and to process sour crudes it needs hydrotreating capabilities, meaning that some simple refineries only have the capacity to refine light sweet crude. More complex refineries are configured to handle higher volumes of heavy crude. These refineries can still process light crude, but less efficiently.
Crude oil streams from different locations have different API gravities and sulfur contents: the price per barrel of a particular oil stream depends on these qualities. The “price per barrel” of oil (when discussed in the United States) usually refers to the price of the West Texas Intermediate (WTI) blend, a light, sweet crude stream produced mostly in the midwest and Gulf Coast regions of the United States. (The WTI is also used as an international benchmark for crude oil prices, along with the Brent Blend—light and sweet, from offshore wells in the North Sea—and the Dubai/Oman Blend—light and sour, used as a price marker for Persian Gulf exports.)
Other important U.S. crude streams are the Light Louisiana Sweet blend, which is light and sweet and produced on the Gulf Coast, and the Mars blend, which is light and sour and produced offshore in the Federal Gulf of Mexico. Important Canadian crude streams are the Mixed Sweet Blend (light and sweet, produced from conventional wells in the Western Canadian Sedimentary Basin) and the Western Canadian Select (heavy and sour, a mixture of bitumen from the Albertan oil sands, several different heavy conventional crude streams, and sweet synthetic crude). Mexico produces mostly Maya Crude, a heavy, sour blend from large offshore fields in the Bay of Campeche. It also produces two lighter blends: Isthmus (light and sour) and Olmeca (light and sweet), mostly from onshore production in the southern states of Tabasco, Chiapas, and Veracruz.
The United States is a net importer of crude and a net exporter of refined petroleum products. Over the last two decades, refineries on the U.S. Gulf Coast (which has more than 50% of the country’s refineries) have invested heavily in configurations to produce high-value product streams from cheaper sour and heavy crude slates, like those traditionally imported from Canada, Mexico, and Venezuela. As heavy sour crude production from the Canadian oil sands has increased over the last decade, many midwestern U.S. refineries have also upgraded to process heavy crude: the Keystone XL pipeline would have provided a direct route for the transport of Western Canadian Select from Hardisty, Alberta to Steele City, Nebraska, for subsequent transport to nearby refineries. 8 Refineries in the northeastern U.S. are still largely configured to refine lighter, sweeter crude slates.
Refineries in western Canada are mostly designed to process a light, sweet crude slate, while refineries in eastern Canada rely more heavily on imported crudes and therefore are designed to process more diverse slates. Almost all of Canada’s crude oil exports go to the United States, primarily from Western Canada to the Midwestern US; the U.S. also exports some crude to eastern Canada.
Only three of Mexico’s six refineries have coking and desulfurization capacities, meaning that the country has limited refining capacity for heavy, sour crude. Since most of Mexico’s petroleum production is in the form of Maya Crude (heavy and sour), the country has historically been a net exporter of crude (mainly to the United States) and a net importer of refined petroleum products (almost entirely from the United States). In August 2015, the U.S. Department of Commerce authorized U.S.-Mexico crude oil swaps, allowing Mexico to trade heavy, sour Maya crude in exchange for light, sweet Eagle Ford crude, in order to better meet each nation’s refinery needs. 9
* * *
What is the future of North American energy production? The trend is clearly towards unconventional oil, but unconventional oil production generally requires high oil prices to be profitable—and right now, oil prices are extremely low. (Oil sits just below $30 per barrel in January 2016, compared to $116 per barrel in April 2011.) U.S tight oil production has slowed dramatically in the last year, especially in the Bakken, where producers break even at about $60 a barrel. Oil sands production is even more expensive—oil must sell for more than $90 a barrel for companies to profit—which means less investment in oil sands until oil prices rise again. Also, the rejection of the Keystone XL pipeline means that a large portion of the crude production from Canadian oil sands must be transported by rail rather than pipeline, which adds almost $10 per barrel to the total cost of production.
Oil prices are likely to remain low: global production continues to outpace demand, with an average production surplus of 1.8 million barrels per day. Meanwhile, OPEC continues to produce well above quota: in 2015, OPEC nations produced about 1.5 million barrels per day in excess of their 30 million barrel-per-day quota. So for the time being, unconventional oil production in North America will continue to decline, at least until oil prices rise again.
1 “Proved reserves” are the most conservative estimates: they only take into account the portion of oil within known reservoirs that can be profitably extracted using existing technology, with about 90% certainty.
2 Mexico expropriated all its oil reserves in 1938 under president Lázaro Cárdenas, and Pemex—the state-owned petroleum company and the sole petroleum company operating in Mexico—lacks the resources to invest in unconventional oil extraction technology. So, unlike the United States and Canada, Mexico has not yet begun to exploit unconventional oil reserves—although a 2014 constitutional amendment, allowing foreign oil companies to operate in Mexico, may change things.
3 There are three types of natural reservoir drive, which can occur separately or in combination: solution gas drive, gas cap drive, and water drive. Solution gas drive requires a reservoir to be fully encased in impermeable rock. When a well is drilled into the reservoir, pressure decreases allowing gas previously dissolved in the oil to escape. The increased volume of the exsolved gas exerts pressure on the oil within the reservoir, driving it upwards through the wellbore. Gas cap drive occurs in reservoirs that contain more gas than can be dissolved in the oil: in these reservoirs, a layer of free gas sits on top of the oil. When the well is drilled and pressure drops inside the reservoir, the free gas above the oil expands, exerting downward pressure on the oil and pushing it up through the wellbore. Water drive requires the presence of an aquifer beneath the petroleum reservoir. As reservoir pressure decreases, the compressed water within the aquifer expands upward to replace the oil, maintaining constant pressure in the reservoir. Water drive is typically the steadiest form of reservoir drive and produces the most prolific oil wells.
4 Oil sands and oil shale are extremely inefficient resources. The average energy return on investment (EROI) for conventional oil is about 25:1, meaning that twenty-five units of oil-based energy are gained for every one unit of energy used to obtain it. The EROI for tight oil is about 20:1, while the EROI for oil sands is only about 5:1, and the EROI for oil shale is expected to be around 3:1 or 4:1 at best.
5 In the petroleum industry, density is measured by American Petroleum Institute (API) gravity, a scale in which water is given an API gravity of 10°. (Liquids with an API greater than 10° are heavier than water.) Extra heavy crude has an API gravity of less than 10°; heavy crude has a gravity between 10° and 22.3°; medium crude has a gravity between 22.3 ° and 31.1°; and light crude has an API gravity greater than 31.1°.
6 The hydrocarbons in crude can be divided into three main categories: paraffins, naphthenes, and aromatics. Paraffins make up 15-60% of crude, can form straight or branched chains, and have a hydrogen to carbon ratio of 2:1. Naphthenes, or cycloparaffins, can make up 15-60% of crude and also have a hydrogen to carbon ratio of 2:1; they are cyclic compounds and are denser and more viscous than equivalent paraffins. Aromatics are also cyclic compounds and even more viscous. They have a slightly lower hydrogen to carbon ratio than paraffins and naphthenes, make up 3-30% of crude, and are less desirable in crude because they produce soot when combusted.
7 The higher the octane number of gasoline, the more compression the fuel can withstand before self-igniting. High-performance gasoline engines require higher compression ratios and therefore higher-octane gasoline. A low octane rating relative to the engine’s compression ratio will lead to “engine knocking,” in which combustion occurs at the wrong point of the four-stroke cycle, causing a dangerous spike in cylinder pressure. From the 1920s to the 1970s (in the US), tetraethyl lead was used as the primary octane booster/anti-knocking agent, until it was banned because of its neurotoxic effects on humans.
8 The original Keystone pipeline, completed in 2010, already transports crude from Hardisty to Steele City by an indirect route, and then continues to Cushing, Oklahoma to the south and Patoka, Illinois to the east. The Keystone pipeline Gulf Coast extension was completed in 2014, running from Cushing, Oklahoma to Port Arthur, Texas.
9 The United States has had an export ban on crude since 1975, after the Arab Oil Embargo. (Crude exports to Canada for domestic consumption were exempted from the ban.) In December 2015, the export ban was lifted entirely.